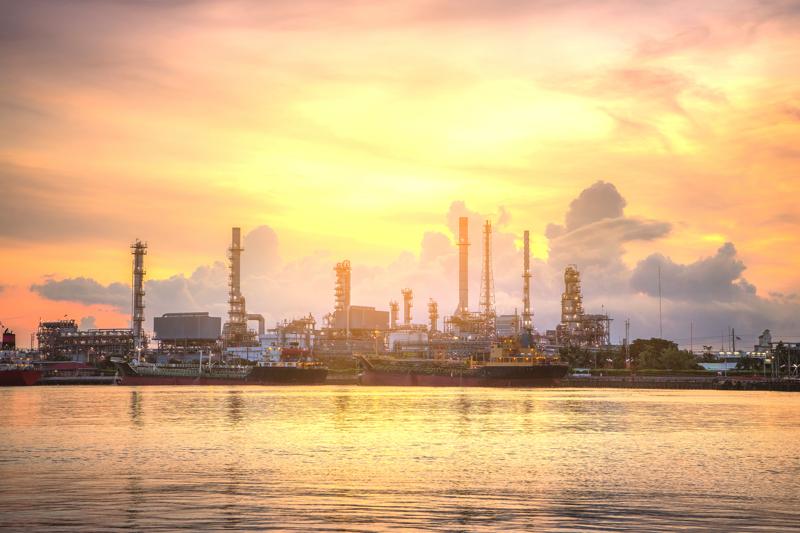
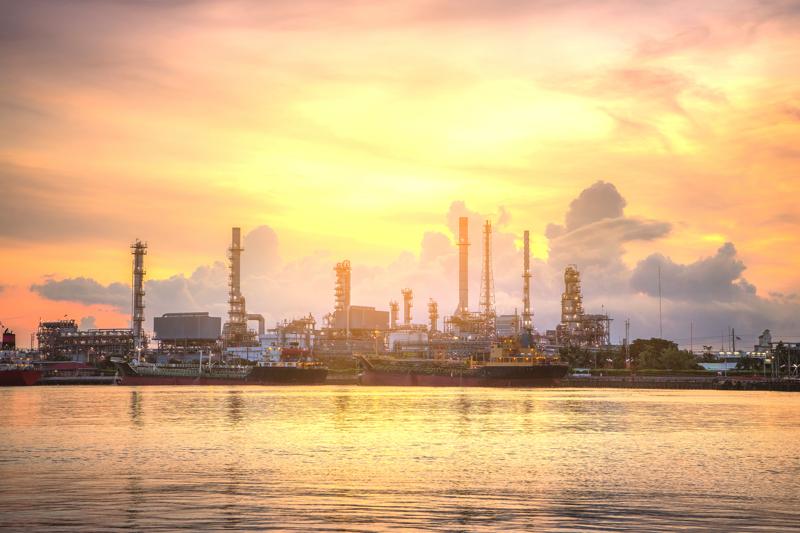
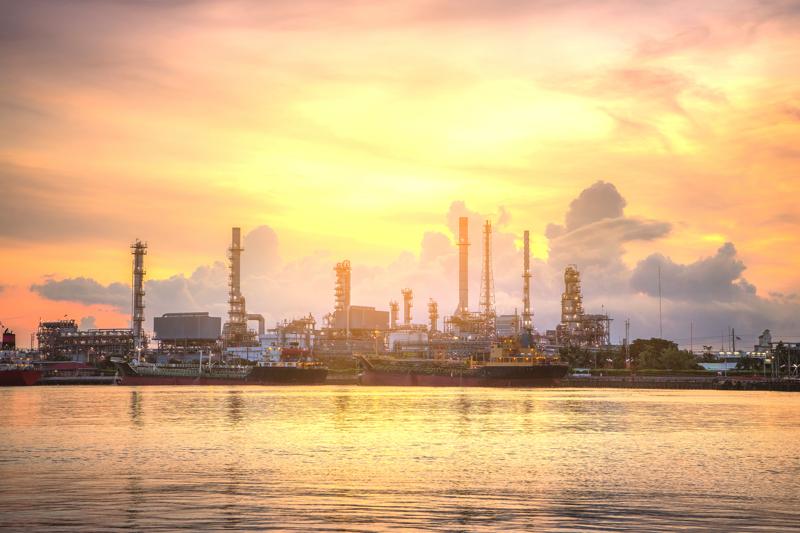
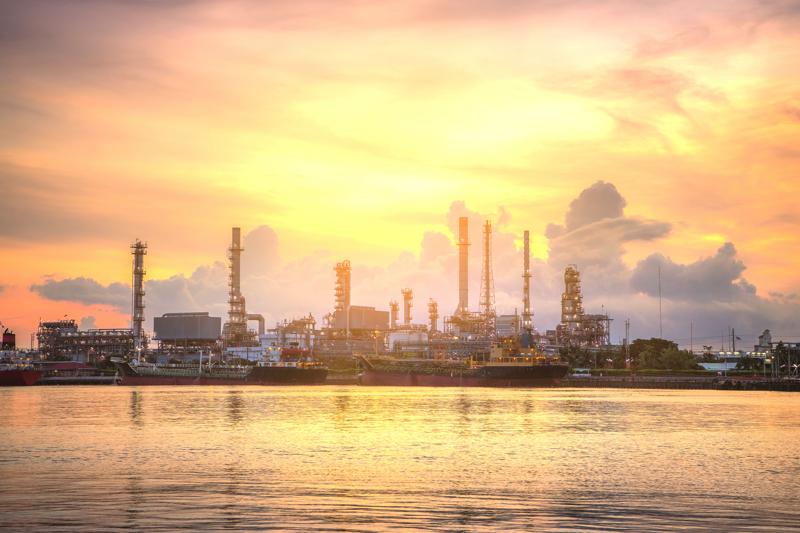
Maintaining full production despite summer heatwaves : Aggreko's tailored cooling solution for chemical plants
Client: Chemical plant
Location: North of Germany
Sectors: Petrochemical and refining
The challenge
Overcoming heat-induced production slowdowns
Our customer, a leading global player in the chemical sector, faced a significant challenge during the latest summer months. Their current dry cooler system faced challenges in coping with the unusually high temperatures and forced production slowdowns. This recurring issue posed a significant threat, as the plant was at risk of reducing output during a critical production period. With rising temperatures potentially leading to substantial financial losses, this chemical plant needed a reliable cooling solution to prevent production cuts and maintain operational efficiency.
Fact File Heading
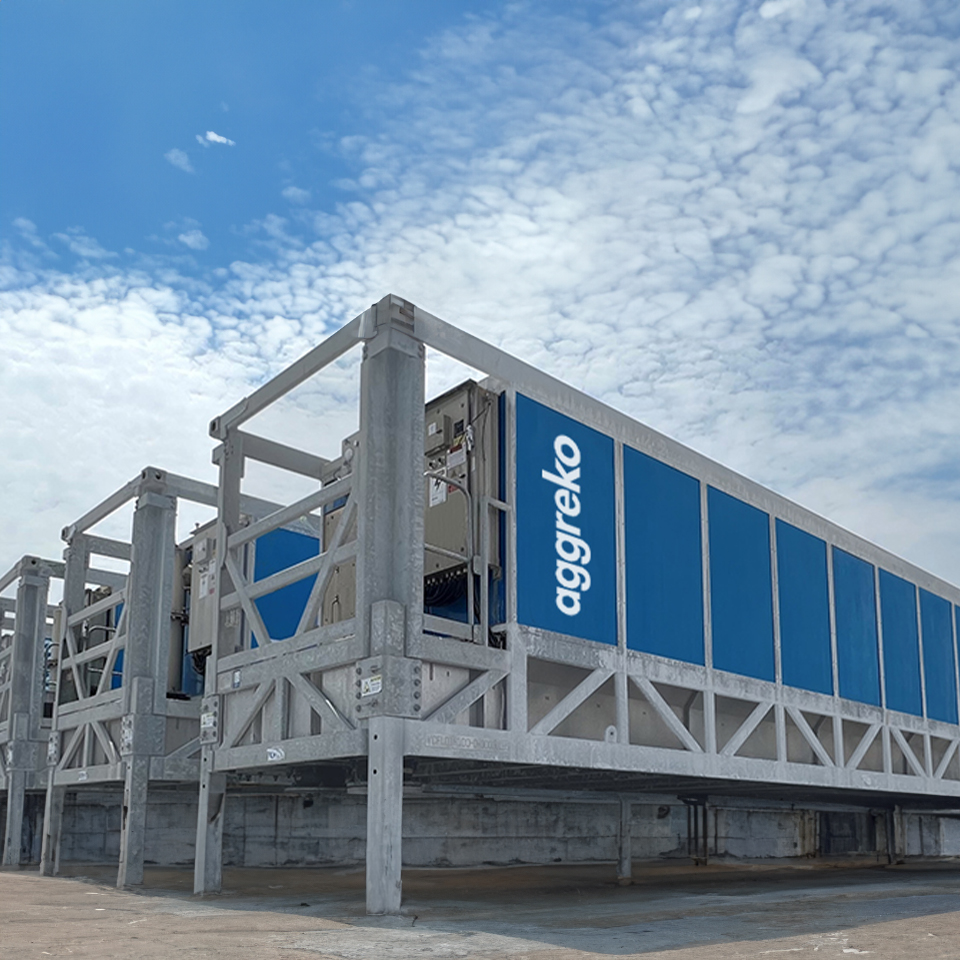
The solution
Bespoke cooling equipment delivered in record time
To address these urgent needs, Aggreko quickly devised a custom solution. After a thorough analysis of the situation, Aggreko provided four advanced cooling towers and four 500 kVA heat exchangers, specifically designed to reduce the temperature of the company’s production equipment during heatwaves. Additionally, Aggreko deployed 600 kVA Stage V generators to ensure the necessary power was delivered to the cooling systems, even under extreme conditions. This equipment was carefully selected and configured to stabilise production, maintaining the required temperatures.
In just two weeks, Aggreko worked closely with this chemical plant to understand their needs and develop the solution, which was then installed and operational within a week – an impressive response time given the scale of the project.
The impact
Preventing downtime and securing financial savings
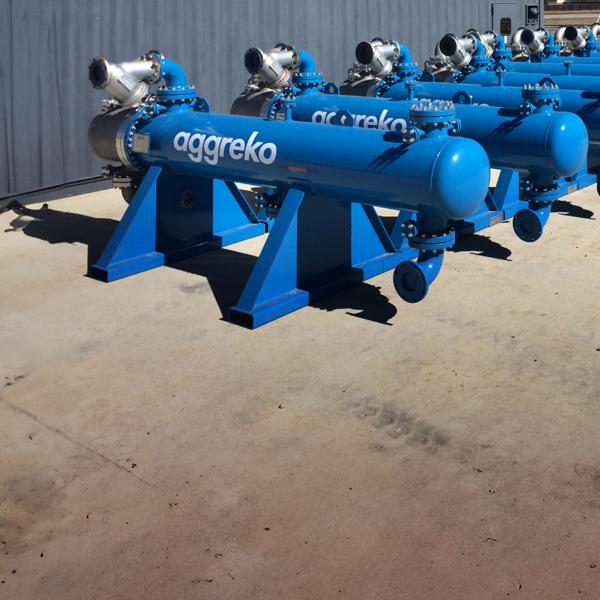