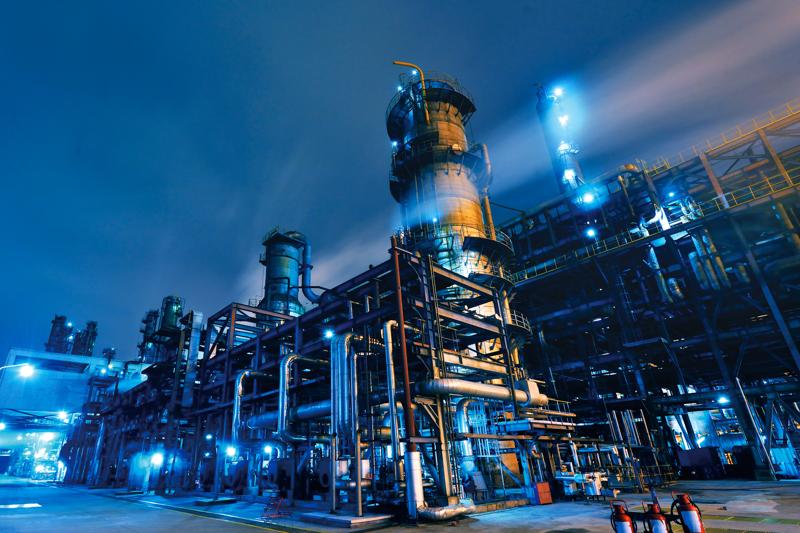
Reducing emissions during refinery maintenance
Client: Mid-continent refinery
Location: USA
Sectors: Petrochemical and Refining
The Challenge
Find a reliable, low emissions fuel during refinery maintenance
A mid-continent refiner was about to go through a significant overhaul and maintenance process but was concerned about increased emissions during that time. Similar turnarounds in the past had used diesel fuel but environmental leaders in the company were keen to explore alternatives given the high emission rates associated with diesel.
They were also concerned about power reliability during heat stress relief applications: this is a process that, once started, you don’t want to stop, due to flow-on impacts to so many activities and people. What would we suggest was the best power system to meet all these complex and interrelated requirements?
Key Facts
80%
$250,000
75% fewer services
The Solution
Replace diesel generators with natural gas generators
The refinery was initially intrigued by our suggestion that they change to natural gas for their fuel source, and then enthusiastic when we pointed out that it would reduce emissions while saving them money.
We produced a full blueprint for our innovative approach and presented the necessary one-line plans. The customer said “Let’s do it” so we went ahead with replacing the diesel generators with gas generators. Our Aggreko Remote Monitoring (ARM) system was used to monitor the set-up for the entire turnaround. This was a particularly vital service during the heat stress relief application process.
The entire project went without a hitch. Savings in dollars and emissions were made and the customer went home happy.
We don’t just deliver the equipment you need. We can also advise on environmental issues and ways to improve your operation.
Aggreko
The Impact
Decrease in emissions, increase in savings
The natural gas generators reduced nitrogen oxide (NOx) emissions by 80 percent, a vast improvement for a refinery that always sailed close to the wind when it came to permitted emission levels.
The refinery saved $250,000 in fuels costs while also avoiding the logistical hassle of frequent diesel fuel deliveries and risk of diesel spills. The gas generators also only needed a service every 30 days compared to diesel generators which required two to three times that amount of attention. Reduced service time meant both cost savings and more time to spend on maintenance tasks rather than support tasks.