Keeping a mill running during a turbine repair
- The Challenge
Keep things running when a key turbine fails
- The Solution
Bring in temporary power - fast
- The Impact
Preventing a shutdown with temporary power
Client:A large mill for hardwood, tissue, and pulp
Location:Maine, US
Sectors:Pulp and Paper
The Challenge
Keep things running when a key turbine fails
Like most mills in the industry, this Maine-based paper and tissue mill relies heavily on renewable energy sources. It can only draw 20 MVA of power at any time from the local utility provider. So, when a 25 MW steam turbine went down, the plant was suddenly left without the power it needed to run full production. Worse still, the turbine had failed just two weeks before the plant’s annual maintenance outage, throwing off a maintenance schedule that had been in the works for months.
Luckily, Aggreko’s local team had engaged with the Mill years ahead of the event for contingency planning for their critical utilities. The Mill identified this 25 MW Steam Turbine as an area of concern within their power distribution system. With Aggreko’s engineering support, we collaborated on a power contingency plan in the event of the Steam Turbine going down. The pulp and paper company asked Aggreko to step in and mobilize the contingency plan natural gas driven generators to keep the mill running while they fixed the turbine.
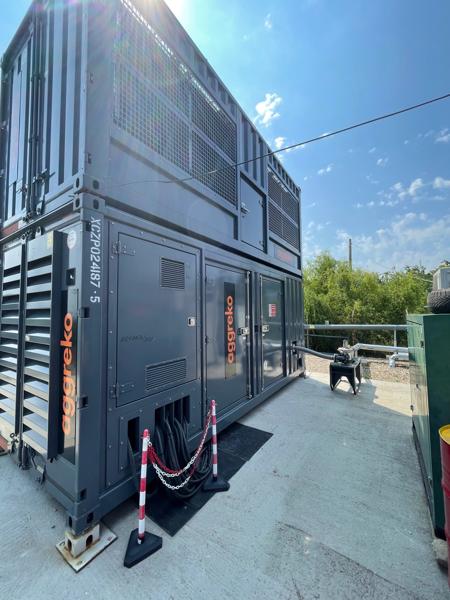
The Solution
Bring in temporary power - fast
Almost as soon as the turbine failed, the plant reached out to Aggreko for help. To limit lost production as much as possible, they asked us to get them up and running again before their annual maintenance outage came to an end. After our engineers had spoken to the team on the ground and assessed their energy and production needs,we stepped in with seven 1.3 MW temporary gas-powered generators - a low-cost, safe, and more environmentally friendly option compared to diesel. Our power plant was specifically engineered to synchronize to the 13.8 kV Mill Buss and other generation assets within the Mill. Aggreko was able to bring the generators online without interrupting other generation or any of the planned maintenance taking place.
The Impact
Preventing a shutdown with temporary power
In a situation like this, most plants would be forced to curtail operations while the turbine was repaired. Instead, we worked closely with on-site engineers to install temporary generators with no impact on the plant’s annual maintenance outage schedule. By installing the generators during the outage, we were able to get the mill running at full capacity in just 11 days. Thanks to the power and reliability of our generators, the plant continued to use them for several months while the turbine was fully assessed and repaired.